STAGE II: PRODUCTION
STAGE II: PRODUCTION
The designing stage has completed!
The production of your order can now start. We are very well prepared for this stage: we set solid foundations, excluded all the spotted defects, minimized the risk of failures and optimized – so far, on paper – the entire production process.
Now, the time has come to switch from theory to practice. In this tab, we will cover the production process of your element in detail.
INJECTION MOULDING ROOM
Have you noticed how many checks, tests, simulations and verifications we have performed so far? A meticulous approach takes time, but on the other hand, it saves your money. The production of your element will be seamlessly performed according to the carefully prepared plan. Before it happens, however, we will test the injection mould.
TEST INJECTION
The test injection, or the test of the injection mould, is performed in the presence of the toolroom and injection moulding room managers and a quality controller. They check whether the tool works properly and whether the prototyped moulded piece meets all the requirements, e.g. whether its weight and dimensions are correct, the structure of the material is even, and the surface has the desired finish. If we consider that some improvement can be made, we will modify the injection mould. It has to be perfect! Later, the approved element is sent to you. Only your final approval gives us the green light to consider the injection mould fit for production, and to create for your element a product data sheet specifying the injection parameters.
FIRST PRODUCTION SERIES
The actual production starts while being constantly monitored by us. At this stage, we verify whether everything goes as planned: the injection machine operator and the quality controller check the weight, dimensions and colour of the element in a special TQC chamber and compare the produced moulded piece with the master piece. If no discrepancies are detected, the mould is approved for the large series production which is subject to the monitoring by our employees. We prefer each subsequent series to be produced with the same injection machine. We choose one, among 19 modern machines, already at the planning stage. Thanks to this, we can ensure the most accurate repeatability and avoid offsets from the established parameters of the element. It means you will receive exactly what you ordered.
ONGOING COOPERATION
The injection mould manufactured by us is a robust tool that will remain fit for production for many years. You can use it whenever you need a new batch of your elements. You can place an order any time, and we will manufacture a new batch of your moulded pieces for you. We can adjust to your current financial and warehouse capabilities and conditions on your market. Thanks to the digital order planning process we have been fine-tuning for several years, we can automatically program the start date of the fulfilment of any incoming order. It allows us to plan our production as to secure your inventory, guarantee an uninterrupted production according to your terms and a timely delivery.
Injection moulding is a process that allows for the production of any plastic element.
Are you curious how does this process look like step-by-step? Have a sneak peek at how your vision becomes reality!
1
The operator mounts the tool onto the injection machine, and the technologist sets the injection parameters according to the product data sheet.
2
A pneumatic feeder sends the specialist mixture of liquid plastics, dye and additives to the feeding hopper zone.
4
The injection mould comprised of two (or more) parts closes with the force of tens or hundreds of tons (a huge force, which is why our tools have to be so accurately and precisely made)!
3
When subjected to the rotation of the screw and high temperature (180–320°C), the material becomes viscoelastic (i.e. gets liquefied), blends with dyes and additives and accumulates in the front of the screw.
5
Under very high pressure, the plasticized mixture is injected to the mould cavities – chambers in the shape of your element.
6
The feed of plastic stops, and the machine waits for the moulded piece to cool down thanks to a special cooling agent. It turns solid again.
8
The injection cycle (points 4 to 7) lasts from 15 to 35 seconds. When finished, the injection machine starts another one. Your moulded pieces are transported to the assembly department.
7
The mould opens, and the finished element is released by an ejector, compressed air and/or a manipulator.
STAGE II: PRODUCTION
Go back to the previous stage

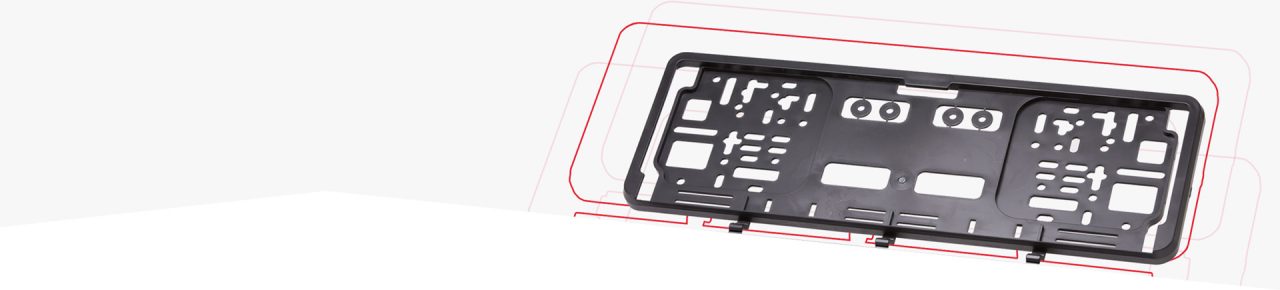