Stage I: designing
Stage I: designing
At Gieros, the designing stage always precedes the production. Even if you already have a finished design, we will analyse it to check whether it can be optimized for production. We believe that preliminary designing assumptions determine the entire subsequent technological process, its effectiveness and profitability, as well as the durability of the injection mould and the final quality of moulded pieces. At this stage, we run economic and technological analysis of your order, we choose the material and the method of production of the injection mould, build prototypes and prepare the documentation. It ensures that the actual production will run smoothly.
Technologgical analysis
of the element production
Usually, an externally-prepared design accounts for one technological option only with established parameters for the injection mould and the moulded piece. Consequently, there is only one price quote. In this scenario, we would act according to the guidelines; next, you would make the payment; and the cooperation would be over.
However, you already know that more options exist. Simultaneously to the estimation of the investment amount, each order is analysed for its feasibility. Our analysis covers the following:
- element size – does our machine park meet your requirements regarding the injection volume?
- production volume – is the production of the estimated number of moulded pieces feasible for the multi-series injection technology?
- element construction – does the construction of your element qualify for the production with injection machines?
- technological feasibility of the design – do the estimated parameters of the element meet the requirements determined by the injection method?
- material – do we process the material you proposed at our plant?
Having a team of designers, constructors, technologists and operators in-house, we can immediately assess whether you design assumptions are feasible for our plant.
Where limitations are found, we can propose you different solutions, as good as yours or better, which are adjusted to your particular situation, e.g. a re-design of the documentation, a size reduction of your element or its division into a few smaller pieces, a material change not impacting the moulded piece parameters, or an increase/decrease in the number of cavities of the mould.
In short: we check, calculate, discuss and ask questions. It may turn out that your designer’s assumptions can be changed for cheaper, faster and smoother production. And maybe instead of spending money on an element with pre-established parameters, you will be able to produce a cheaper but equally functional one, and reallocate savings to a more efficient mould. This will allow you to produce more moulded pieces cheaper, sell them with profit and earn even more than you expected. Isn’t it what counts most for you?
STAGE I DESIGNING
GO TO A DIFFERENT SAGE

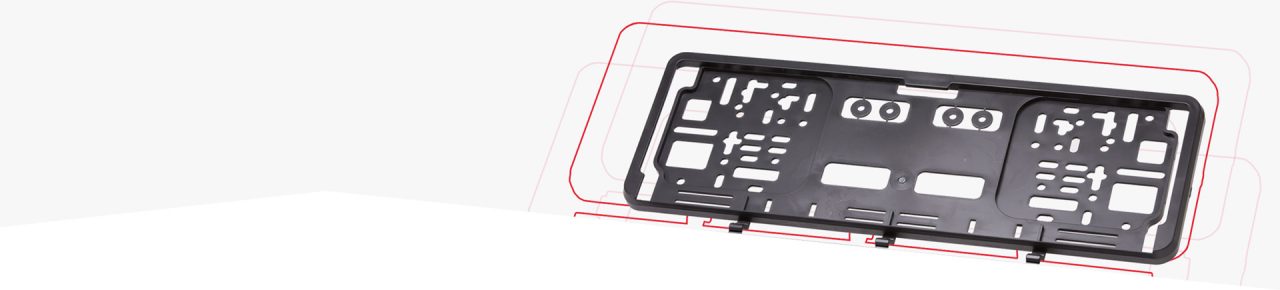