STAGE II: PRODUCTION
STAGE II: PRODUCTION
The designing stage has completed!
The production of your order can now start. We are very well prepared for this stage: we set solid foundations, excluded all the spotted defects, minimized the risk of failures and optimized – so far, on paper – the entire production process.
Now, the time has come to switch from theory to practice. In this tab, we will cover the production process of your element in detail.
TOOLROOM
You already know our toolroom. In this area, we perform all the designing and analytical tasks which allow for the planning and optimization of the actual production of your order. Also here, the indispensable tool is constructed.
However, before explaining its creation process, we would like to provide you with basic information about injection moulds.
An injection mould is a highly complex tool. It consists of several interacting systems such as mounting, material feed, cooling and moulded piece release systems and other, determined by your product. It is divided into two or more spheres and build of several dozen, or even several hundred, elements which we manufacture with the utmost precision (alternatively, we may buy them at highly specialized producers which whom we partner, e.g. Hasco, Stäubli, Meusburger).
Each element has to be drawn, measured and assessed in terms of interaction with other elements, as well as the impact on the moulded piece; also, it has to be tested. It would have been impossible without our craftsmanship and solid expertise
1
CREATION/VERIFICATION OF YOUR ELEMENT
You already know a lot about this process. There are several scenarios: you can already have a design which can be adjusted to the planned production process; or have just an idea for an element which will be visualised and adapted to our technological capabilities. At this stage, we will also prepare a virtual simulation of the injection in SolidWorks Plastics software and 3D-print a prototype. Thanks to these preparation works, we can identify issues of the moulded piece, implement corrections and your suggestions, and eliminate errors which may later generate costs both on our and your end, to the highest extent possible. The result of the above works is a professionally prepared design of your element.
2
DESIGNING THE INJECTION MOULD
Once the element design is ready and fully polished, the next step is to design the injection mould which will allow for its production. We start with establishing some basic principles: what material should the tool and the cavity plates be made of (steel or aluminium)? Which is the desired mould multiplicity (or the number of cavities corresponding to the number of moulded pieces produced in one production cycle)? What is the estimated production volume and the lifespan of the tool? We gather these information in order to plan the technology for the production of the tool. You can rely on our thorough experience in this matter. We produced almost 1500 injection moulds and counting!
4
CNC
MACHINING
At this stage of works, we can finally demonstrate the capacity of our toolroom fully. In our machining centre there are 6 CNC HAAS machines. A forming plate necessary for the fulfilment of your order is produced with one of them. In simple words, the actual production process of your injection mould with the CNC machining method will now start. Once finished, each element will be assessed in terms of, for example, surface finish parameters or the compliance of the obtained measures with the estimated ones. For this purpose, we will use traditional metrological tools or a mobile Renishaw probe that each CNC machine is equipped with. Our production standards require the micron-level of precision for the mould to work properly.
3
CNC MACHINES CONFIGURATION
Some elements of the designed injection mould are sourced at the world-class suppliers. The majority of them is, however, produced in-house with our CNC machines which have to be configured for this purpose. Thanks to SolidWorks, a professional software for computer designing, the programmer involved in the fulfilment of your order chooses cavity plates machining type and sets the machining parameters. Before starting the CNC machines, another computer simulation is performed. This time, we test each machining operation and their deliveries. Thanks to this, we can verify the injection mould design and fix any potential defects in advance. Once this stage is completed, a fine-tuned CNC machine programme is ready. The machining process can now start.
5
MOULD ASSEMBLY
The last task performed in the toolroom is the assembly of the injection mould. The toolroom worker carefully assembles all the components of the mould, i.e. pullers (which allow for the safe release of the moulded piece from the injection mould), as well as posts, sleeves, centring systems, locks or sliders, and checks the tightness of the cooling system. At this point, the moulding cavities are also polished or sandblasted which guarantees that the surface finish of your element is exactly as it should be. Once the assembly is finished, the toolroom and injection moulding room managers check the accuracy of the production tool. After its approval a test injection is performed.
IMPORTANT NOTE!
At Gieros, we value partnership with clients. Its core principle is the loyalty, which we guarantee. We guarantee that all the projects made for you are confidential and fully safe at Gieros, and that they will remain your property. It means we will not share nor sell your idea to your competitors. Our cooperation with you will remain confidential, unless you wish otherwise. It even happens that we refrain from working with other companies from our clients’ industries.
This approach stems from our business ethics. We know that a successful cooperation and a shared financial success is based on our clients’ trust.
STAGE II: PRODUCTION
Go back to the previous stage

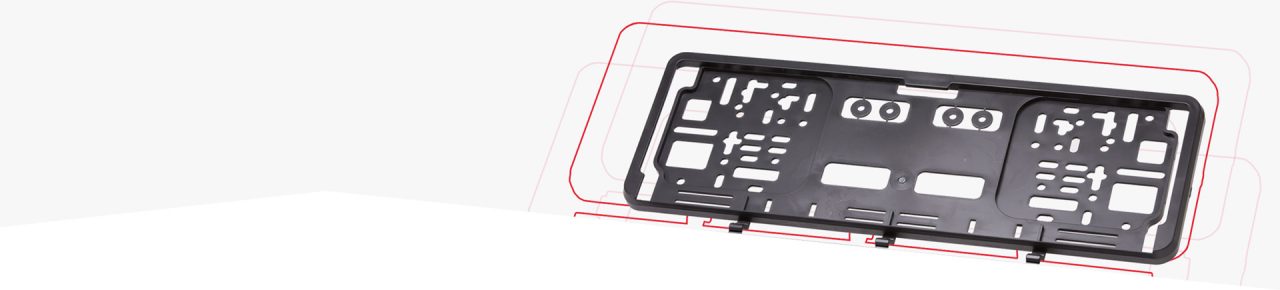